Flexible Graphite Sheets: Unlocking New Possibilities in Industrial Sealing Applications
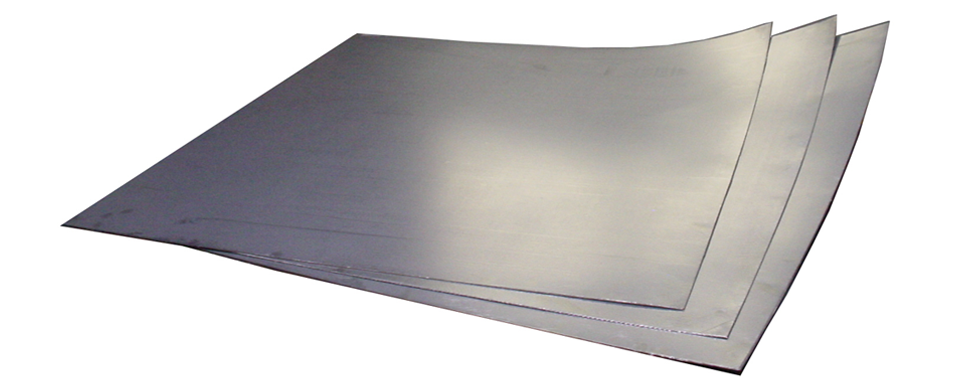
In the realm of industrial sealing applications, where reliability, durability, and efficiency are paramount, flexible graphite sheets have emerged as indispensable tools. These innovative materials, derived from high-quality natural graphite flakes, offer a unique combination of flexibility, thermal conductivity, chemical resistance, and impermeability, making them ideal for sealing solutions in a wide range of industries. From oil and gas to chemical processing, power generation, and beyond, flexible graphite sheets are unlocking new possibilities and revolutionizing traditional sealing practices.
The Evolution of Flexible Graphite Sheets
Flexible graphite sheets represent a significant advancement in sealing technology, building upon the intrinsic properties of graphite while introducing enhanced flexibility and adaptability. Unlike traditional gasket materials such as rubber or cork, which may degrade over time or fail to provide a reliable seal under challenging conditions, flexible graphite sheets offer unparalleled performance and longevity. Their layered structure, composed of graphene sheets arranged in a hexagonal lattice, enables them to conform to irregular surfaces and withstand extreme temperatures, pressures, and chemical exposures encountered in industrial environments.
Versatility Across Industries
One of the key strengths of flexible graphite sheets lies in their versatility across a wide range of industries and applications. In the oil and gas sector, where sealing integrity is critical to preventing leaks and ensuring safety, flexible graphite sheets are utilized in flange gaskets, valve stem packing, and pipeline seals. Their ability to maintain a tight seal under high pressures and temperatures, as well as resistance to corrosive fluids and gases, makes them indispensable components in offshore drilling platforms, refineries, and petrochemical plants.
Similarly, in the chemical processing industry, flexible graphite sheets find extensive usage in equipment such as pumps, reactors, and heat exchangers, where they provide reliable sealing solutions for handling corrosive chemicals, acids, and solvents. Their compatibility with a wide range of media, combined with excellent thermal conductivity, allows for efficient heat transfer and prevents leakage, minimizing the risk of process contamination and equipment failure.
In power generation facilities, including thermal power plants and nuclear reactors, flexible graphite sheets play a crucial role in sealing steam and coolant systems, turbine components, and boiler fittings. Their resilience to high temperatures and pressures, coupled with thermal stability and minimal creep relaxation, ensure long-term sealing performance in demanding operating environments, contributing to the reliability and efficiency of power generation operations.
Innovative Applications and Advancements
Advancements in material science and manufacturing techniques have led to the development of innovative applications for flexible graphite sheets, further expanding their utility and efficacy in industrial sealing applications. Engineered variants, such as reinforced graphite sheets with metal or polymer inserts, offer enhanced mechanical strength and dimensional stability, allowing for tighter seals and reduced flange leakage in critical applications.
Moreover, the introduction of adhesive-backed flexible graphite sheets simplifies installation and improves sealing efficiency by eliminating the need for additional sealants or gasket adhesives. These self-adhesive sheets adhere securely to mating surfaces, forming a tight seal upon compression, and reducing the risk of gasket blowouts or leaks during operation.
Future Prospects and Emerging Trends
Looking ahead, the future of flexible graphite sheets in industrial sealing applications appears promising, with ongoing research and development efforts focused on further enhancing performance, expanding material options, and addressing specific industry challenges. Advancements in nanotechnology may lead to the development of ultra-thin graphene-based sealing materials with superior flexibility, strength, and chemical resistance, opening up new possibilities for sealing solutions in microelectronics, aerospace, and biomedical applications.
Furthermore, the adoption of digital manufacturing technologies, such as additive manufacturing (3D printing), holds the potential to revolutionize the production of complex-shaped gaskets and seals, custom-tailored to meet the precise requirements of individual applications. This shift towards digital design and fabrication methods promises to streamline the development process, reduce lead times, and optimize material usage, ultimately driving greater efficiency and cost-effectiveness in industrial sealing operations.