A Comparative Analysis of Inconel 625 vs. Inconel 718: Which One to Choose for Pipe Fittings?
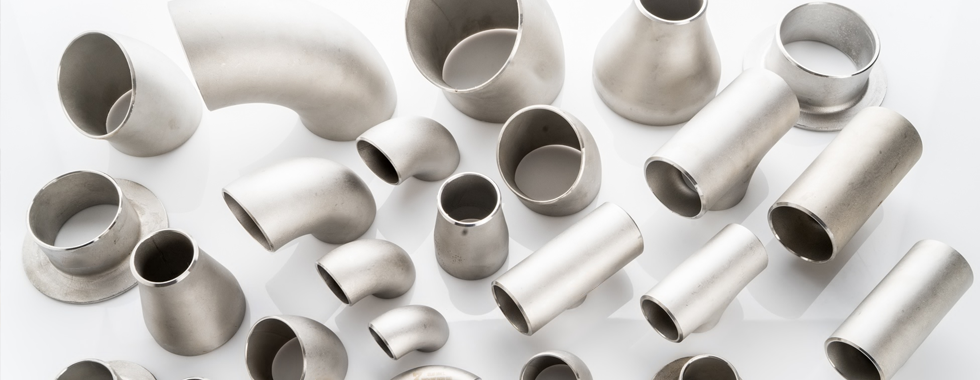
In industries where extreme conditions are the norm, selecting the right material for pipe fittings is crucial. Two popular choices, Inconel 625 and Inconel 718, stand out due to their exceptional strength, corrosion resistance, and durability. This article compares these two nickel-based superalloys, helping you make an informed decision for your pipe fitting needs.
Overview of Inconel 625 and Inconel 718
Inconel 625: Known for its superior corrosion resistance, Inconel 625 is ideal for environments with high temperatures and aggressive chemicals. It is commonly used in applications like chemical processing, marine engineering, and offshore oil rigs.
Inconel 718: This age-hardenable alloy excels in high-stress environments, particularly in aerospace and gas turbines. Its strength and creep resistance make it suitable for applications requiring prolonged exposure to high temperatures.
Key Differences Between Inconel 625 and Inconel 718
-
Composition
- Inconel 625: Higher molybdenum and niobium content enhance its corrosion resistance, especially in seawater and oxidizing environments.
- Inconel 718: Contains additional aluminum and titanium, improving its strength and making it age-hardenable.
-
Strength
- Inconel 625: Offers excellent tensile strength but is slightly less robust than 718 under prolonged high-stress conditions.
- Inconel 718: Outshines 625 in tensile strength, particularly after heat treatment, making it suitable for high-pressure pipe fittings.
-
Temperature Resistance
- Inconel 625: Performs well up to 982°C (1800°F). Ideal for moderate high-temperature environments.
- Inconel 718: Maintains stability up to 704°C (1300°F) under mechanical loads but can withstand higher temperatures in less stressful conditions.
-
Corrosion Resistance
- Inconel 625: Excels in environments with chlorides, acids, and oxidizing agents, making it a top choice for pipe fittings in chemical plants and seawater systems.
- Inconel 718: Good corrosion resistance but not as exceptional as 625 in marine or highly acidic environments.
-
Weldability
- Inconel 625: Easier to weld and fabricate, minimizing the risk of cracking.
- Inconel 718: Welding can be more challenging due to its age-hardening characteristics but can be managed with proper techniques.
Applications in Pipe Fittings
Inconel 625 Pipe Fittings: Ideal for chemical transport, marine systems, and high-corrosion areas. Its excellent resistance to pitting and crevice corrosion makes it a go-to choice for flanges, elbows, and tees in harsh environments.
Inconel 718 Pipe Fittings: Best suited for aerospace, nuclear reactors, and high-pressure systems where strength and creep resistance are paramount. Commonly used for components like reducers and couplings in high-stress pipelines.
Which One Should You Choose?
Choose Inconel 625 if your application requires exceptional corrosion resistance, especially in marine or chemical environments. It’s also a great choice for pipe fittings in systems exposed to fluctuating temperatures.
Choose Inconel 718 if your system operates under high mechanical stress and demands superior strength and durability. It’s particularly suitable for high-pressure pipelines in aerospace or power generation industries.
Both Inconel 625 and Inconel 718 are outstanding materials for pipe fittings, but their unique properties cater to different applications. By understanding your system's requirements—whether it’s corrosion resistance or mechanical strength—you can select the alloy that ensures optimal performance and longevity.
As a leading manufacturer of Inconel pipe fittings, Metallum Overseas specialize in providing high-quality solutions tailored to your industrial needs. From flanges and elbows to reducers and tees, we deliver pipe fittings designed for durability and performance. Contact us today to discuss your requirements or request a quote.