The Role of C80 Spring Steel in Manufacturing and Industrial Machinery
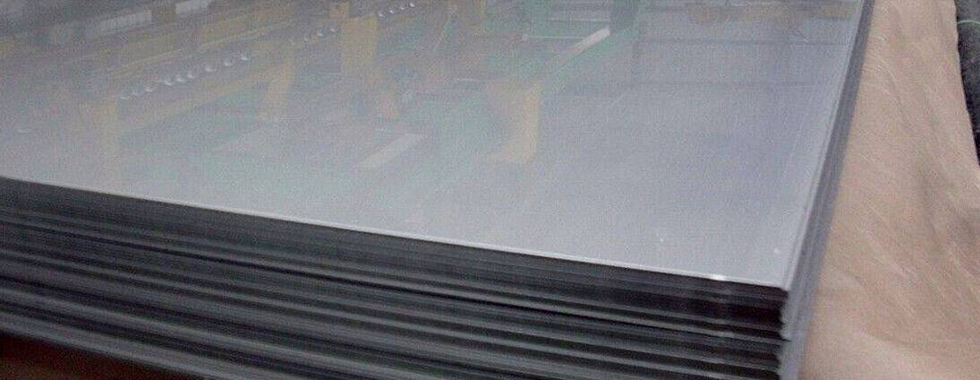
In the dynamic world of manufacturing and industrial machinery, where precision, reliability, and durability are paramount, the role of materials like C80 spring steel cannot be overstated. With its exceptional mechanical properties and versatility, C80 spring steel plays a crucial role in various applications, from stamping dies and tooling to mechanical springs and components in heavy machinery. In this comprehensive article, we delve into the unique characteristics of C80 spring steel, its applications in manufacturing and industrial machinery, and the key factors driving its widespread adoption in the industry.
Understanding C80 Spring Steel: A Material of Exceptional Strength
C80 spring steel, also known as AISI 1080 or 1.1248 steel, is a high-carbon alloy steel renowned for its excellent mechanical properties, including high yield strength, good ductility, and superior hardness. It derives its name from its approximate carbon content of 0.80%, which contributes to its remarkable strength and resilience. Additionally, C80 spring steel exhibits excellent toughness and wear resistance, making it suitable for demanding applications in manufacturing and industrial machinery where heavy loads, cyclic stresses, and abrasive conditions are common.
Applications in Manufacturing Processes: From Stamping Dies to Tooling
One of the primary applications of C80 spring steel is in the production of stamping dies and tooling used in metalworking processes such as punching, blanking, and forming. The exceptional hardness and wear resistance of C80 spring steel make it an ideal choice for manufacturing dies and tooling that must withstand high impact forces, abrasive wear, and prolonged use without deformation or failure. Whether shaping sheet metal components in automotive manufacturing or producing precision parts in aerospace engineering, C80 spring steel dies and tooling ensure consistent quality and efficiency in manufacturing processes.
Moreover, C80 spring steel finds extensive usage in the fabrication of cutting tools, including drills, reamers, and milling cutters, where its high hardness and toughness enable efficient material removal and prolonged tool life. From machining operations in machine shops to large-scale manufacturing facilities, C80 spring steel tools contribute to productivity gains, cost savings, and superior surface finish in metalworking applications.
Critical Components in Industrial Machinery: Springs, Shafts, and Components
In addition to its role in dies and tooling, C80 spring steel is widely employed in the production of mechanical springs and components for industrial machinery. Springs made from C80 spring steel exhibit excellent resilience, fatigue resistance, and load-bearing capacity, making them suitable for a variety of applications, including suspension systems, valve springs, and mechanical actuators. Whether absorbing shocks in automotive suspensions or maintaining tension in heavy machinery, C80 spring steel springs provide reliable performance and longevity in demanding environments.
Furthermore, C80 spring steel is utilized in the manufacture of shafts, gears, and other critical components in industrial machinery, where its combination of high strength, hardness, and wear resistance ensures smooth operation, minimal downtime, and maximum reliability. Whether transmitting power in gearboxes, supporting rotating shafts in bearings, or transferring motion in mechanical systems, C80 spring steel components play a vital role in maintaining the efficiency and functionality of industrial machinery across various sectors.
Key Factors Driving Adoption: Performance, Reliability, and Cost-effectiveness
The widespread adoption of C80 spring steel in manufacturing and industrial machinery can be attributed to several key factors. Firstly, its exceptional mechanical properties, including high strength, hardness, and toughness, make it well-suited for applications subjected to heavy loads, cyclic stresses, and abrasive conditions. Secondly, its reliability and durability ensure consistent performance and minimal maintenance requirements, contributing to overall operational efficiency and productivity. Finally, its cost-effectiveness relative to other high-performance materials makes it an attractive choice for manufacturers seeking to optimize production costs without compromising on quality or performance.